
At Gooseneck, we are continuously striving to find ways to help our technicians become more efficient, so that we can provide our customers with faster solutions. GTAC, Gooseneck Technical Assistance Center, has provided an opportunity for experienced technicians to find a use for their high knowledge while taking on a role that’s less physically demanding than a field technician. Likewise, our technicians have somewhere to reach for assistance if they are struggling to find a solution to a mechanical issue.
GTAC was implemented at Gooseneck in May 2020. Since the start, the GTAC team has found solutions to almost 1,600 tickets with an average time-to-response rate of two minutes. Those numbers prove that the team is committed to finding solutions for our technicians and getting the customer back up and running in an impressive time.
Last week, I sat down with Mike Thorson and Fred Berndt to talk about their experience on the GTAC team.
How long have you been with Gooseneck?
Fred: I started as a Service Department Technician in 2001 and then began with GTAC in April, 2020.
Mike: I started in 1994 as a Service Department Technician and transitioned to the GTAC team in February, 2021.
What is the best part of your job?
Fred: Helping people. I enjoy working through solutions with the technicians and knowing that I was able to help them get home faster.
Mike: The ability to work from anywhere. I’ve been able to pack my stuff up and respond to GTAC calls no matter where I am. That flexibility has been really great.
Have you had the opportunity to solve a GTAC case with the Smart AR Glasses? How was that process?
Fred: Yes – the visual piece of it is a huge help. It takes the work out of your mind’s eye and puts the exact issue right in front of your screen. For GTAC, it has been a great help.
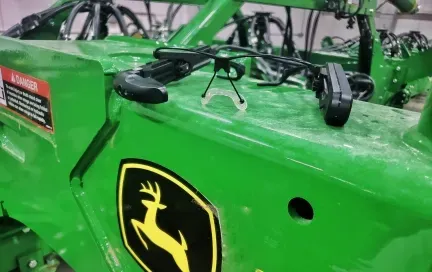
What is it like to have to visualize what these technicians are working on when you aren’t using the glasses? Do you find it challenging to diagnose issues without seeing what the technician is working on?
Mike: It is definitely challenging. If we aren’t able to provide a solution through our knowledge alone, we are able to do research on the issues while the tech is out in the field. We can pull up the tech manuals, search through parts, and access DTAC (Deere Technical Assistance Center) Solutions to see if we can find the answer for the technician. As part of GTAC it is important for us to take classes and work to grow our knowledge so that we can help our technicians when challenging issues come up.
Do you think GTAC is a good option for older technicians looking for a career transition into something that is less physically demanding?
Mike: That’s why I took the job! It’s challenging and still allows me to use the 30 years of knowledge that I have in a way that helps our technicians and our customers.
Fred: Yes – its challenging and keeps your mind sharp while still allowing you to contribute to Gooseneck. As a technician, you are seasoned to work through a job start to finish. You begin with the issue and you see it the whole way through to completion. Being on GTAC has required me to change the way I see jobs. Now I’m a small piece of the puzzle. I help solve one problem, but I don’t see the machine all the way through to completion. That is what the technician does. For me, I could bounce between a Sprayer and a Combine all within a half hour. You have to retrain your brain to be able to bounce around to different machines and issues in any given moment on any given day.
When you aren’t at work, what do you like to do in your free time?
Mike: I like to take motorcycle trips with my wife. I am a part of the Gallows Club in Towner so we spend quite a bit of time involved with that.
Fred: Watching my kids play sports. They are currently 12 and 14 so they are involved in quite a bit of school athletics.
What is your favorite John Deere Machine?
Mike: I like seeing all of the new stuff. The way that technology is evolving in these machines is exciting.
Fred: The John Deere 4020, a classic.
Do you have any success stories that illustrate how GTAC has helped our technicians?
Fred: This spring I was able to help with a lot of calibration issues on seeders. Our technicians were running into issues and I was able to help them work through them in just a half hour or so.
Employee Testimonials
“Using the glasses so GTAC is able to see what I see to help find a solution was great. The concept to help find the solutions faster for customers is really a positive one.”
-Dustin Volk, Service Technician
“I recently had the opportunity to use GTAC for the first time. I was really happy with the experience and was able to get help with the issue I was having. Calling Fred to find a solution worked really well.”
-Dylan Drader, Service Technician
“GTAC saves a lot of time. We are able to find a solution to the problem we are running into within minutes. There is a lot of knowledge out there through technician experience that we are able to access in ways we weren’t able to before. As a tech out in the field, using the AMS side of things has really been great to help with GPS and Section Control questions”
-Adrian Lemieux, Service Technician
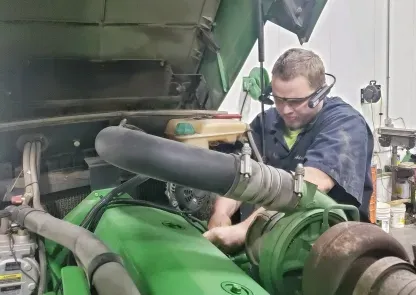
Through GTAC, the use of knowledge and communication brings the ability for technicians to find a solution for customers quicker. This is huge for both parties involved. Customers are able to get into the field quicker and technicians are able to get home to their families sooner, as Fred stated in the interview. Bringing the circle together to improve the experience is what GTAC is all about.
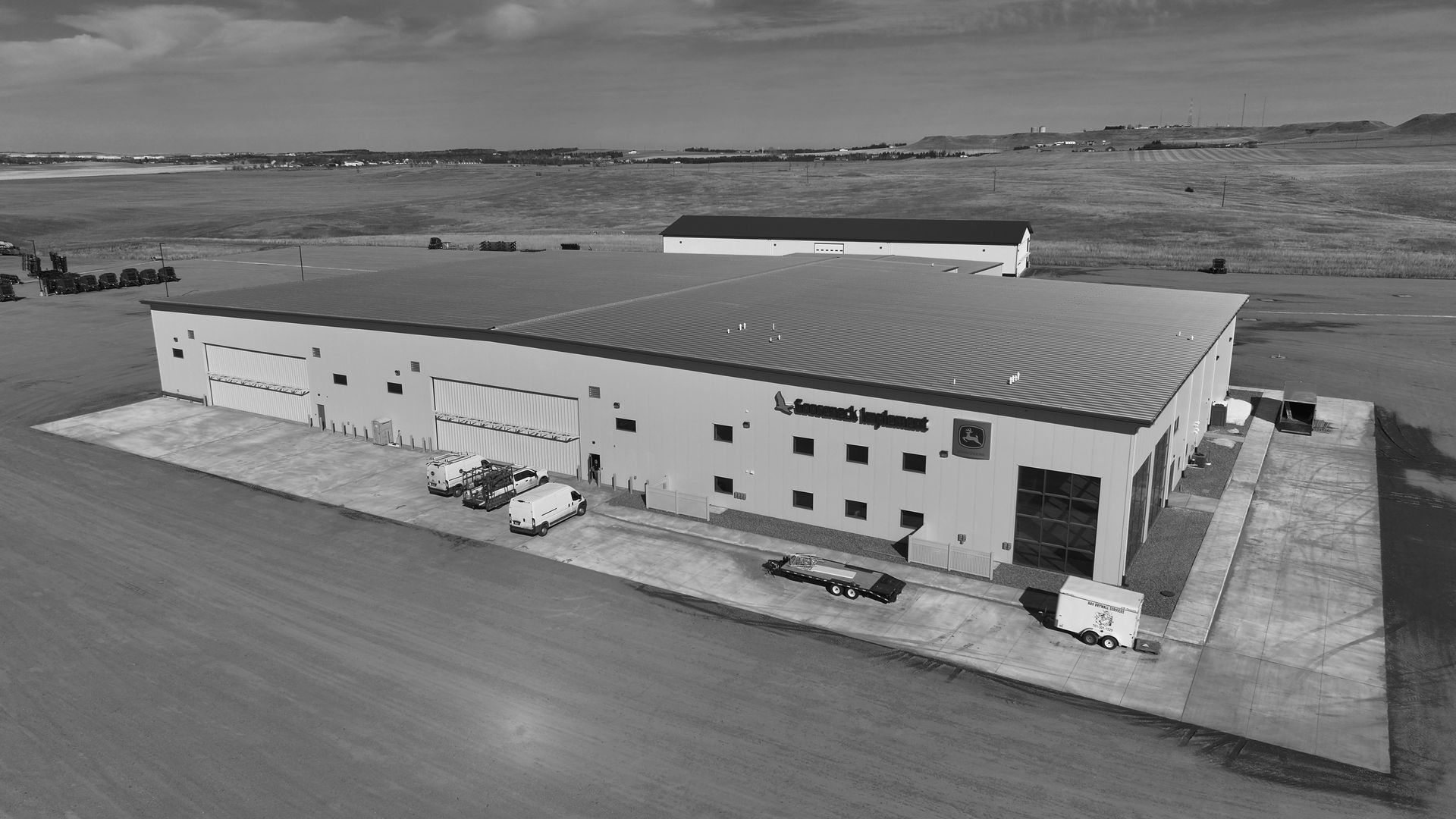
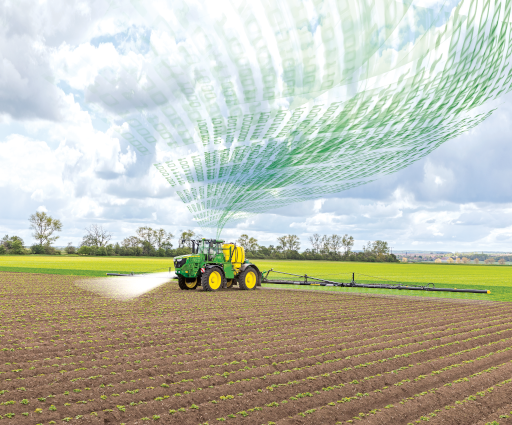